Vibration Polishing Machine
The high-speed vibration drives the abrasive to rub against the workpiece, thus achieving deburring, polishing, cleaning and chamfering surface treatment equipment. It is suitable for finishing of large quantities of parts and is widely used in hardware, electronics, automobiles, aviation, watches and other industries.
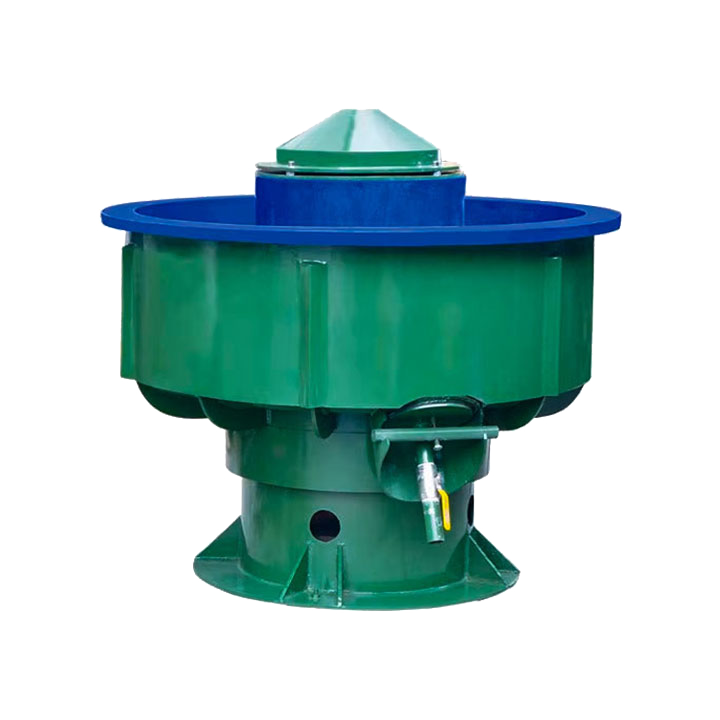
Machine Features
High-frequency vibration drives the abrasive flow to achieve precise polishing.
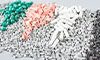
By combining different grinding media and chemical additives, a variety of surface effects can be achieved, such as bright, matte, descaling, etc.
Batch Processing
Process a large number of workpieces at the same time, greatly improving production efficiency.
Uniformity
The grinding medium is in full contact with the workpiece, and the surface treatment effect is consistent, with no omissions and no dead corners.
Various Materials
Whether it is stainless steel, aluminum alloy or copper parts, ideal processing effects can be achieved.
Applicable polishing chemicals
Can be used with various polishing agents, rust removers, brighteners and other chemical additives
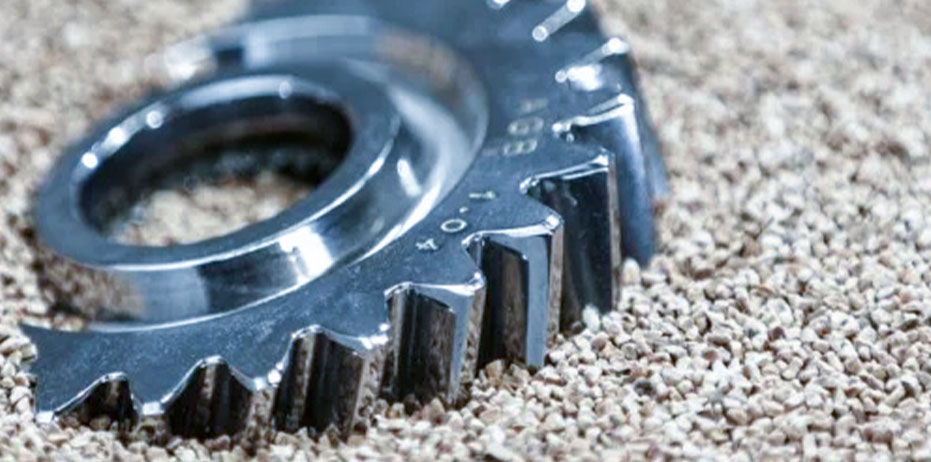
Effortless Polishing for Irregular and 3D Parts.
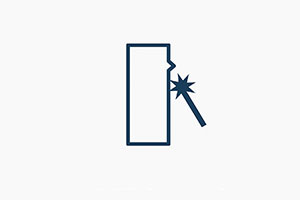
Deburring
Remove burrs and sharp corners generated during part edge processing to improve safety and assembly accuracy.
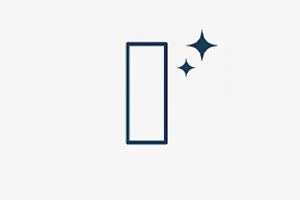
Polishing
The grinding medium is in constant contact with the workpiece surface, making it smooth and improving the appearance quality.
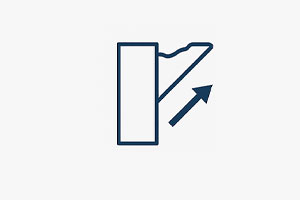
Descaling
Remove the oxide layer formed on the metal surface due to heat treatment or long-term exposure, and restore the original color of the metal.
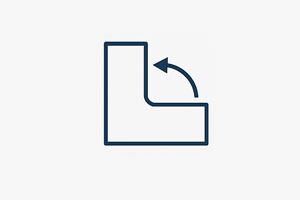
Edge Rounding
Slightly smooth out sharp edges or corners of a part to make it more suitable for assembly, painting, or to prevent scratches.
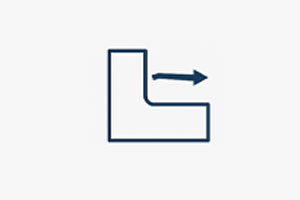
Surface Smoothing
Through continuous impact, the metal surface microstructure is improved, and fatigue resistance and wear resistance are enhanced.
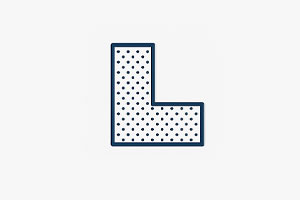
Matting / Satin Finishing
Use specific abrasives to adjust the surface gloss and create a fine, non-glare matte effect.
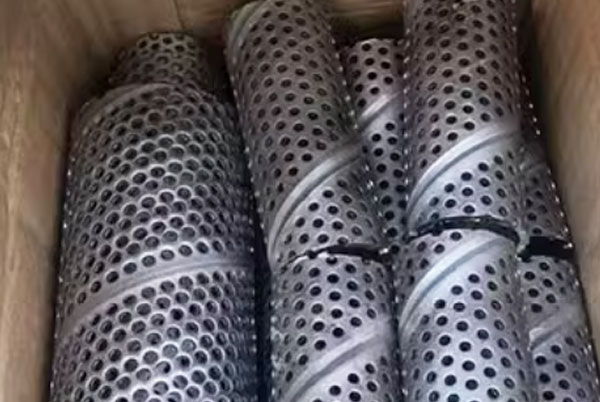
Before polishing
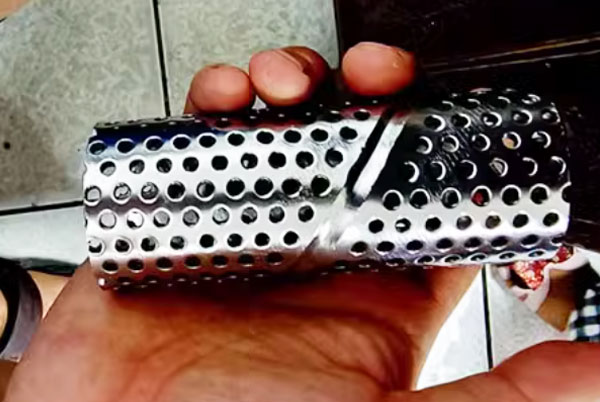
After polishing
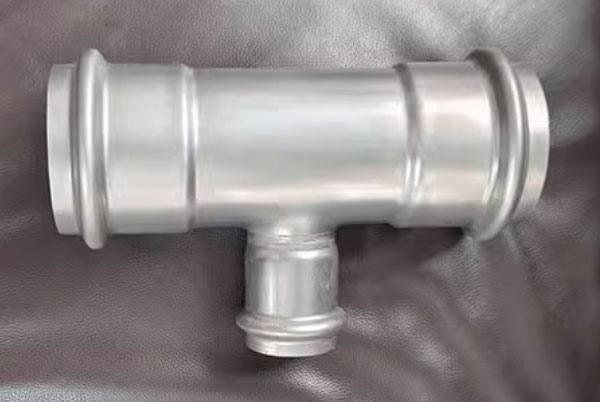
After polishing
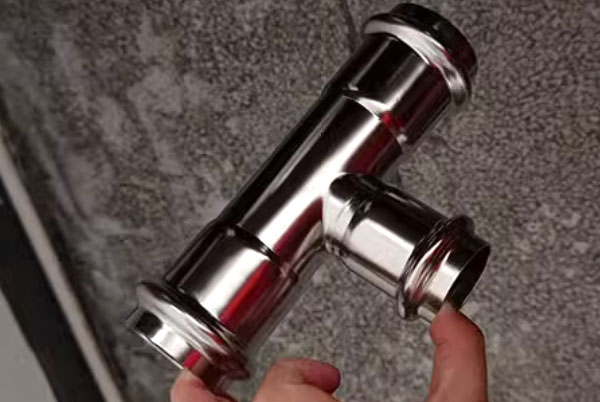
After Sandblasting
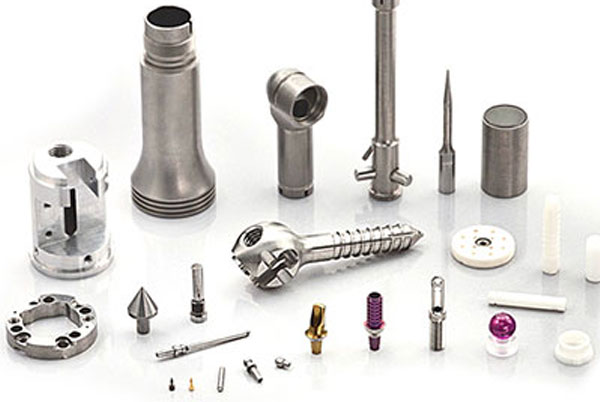
Medical Parts
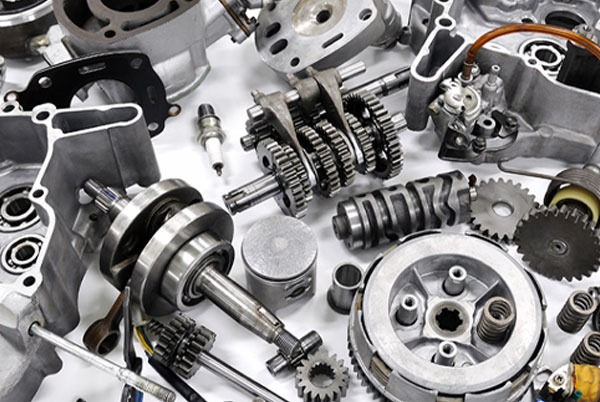
Abrasive Flow Machining of Automobile Parts
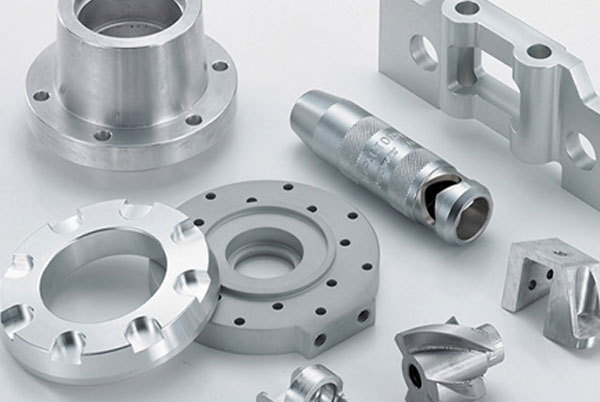
Abrasive Flow Machining of Aerospace Parts
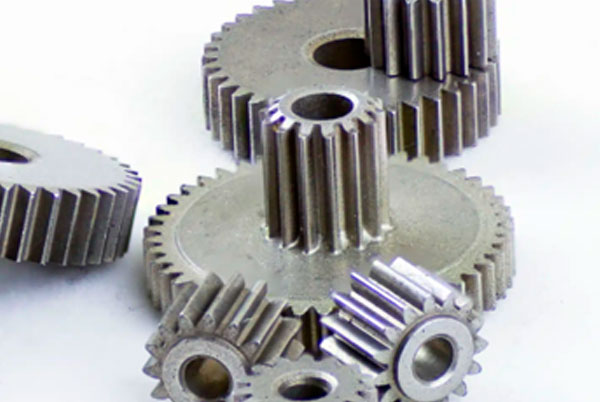
Gear Abrasive Flow Machining
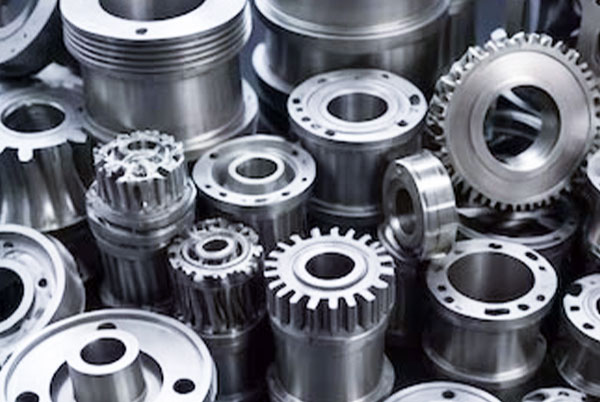
Fluid polishing of precision parts
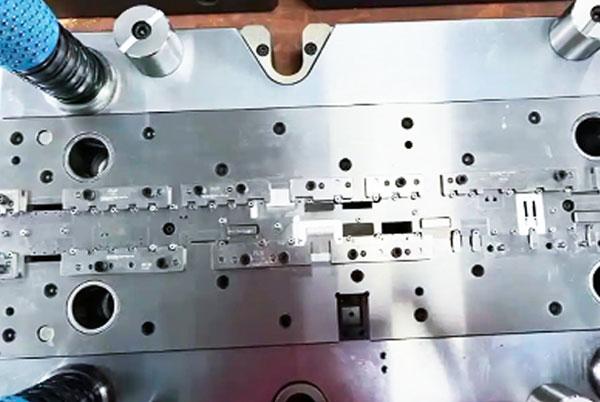
Mold Fluid Polishing

Semiconductor Parts
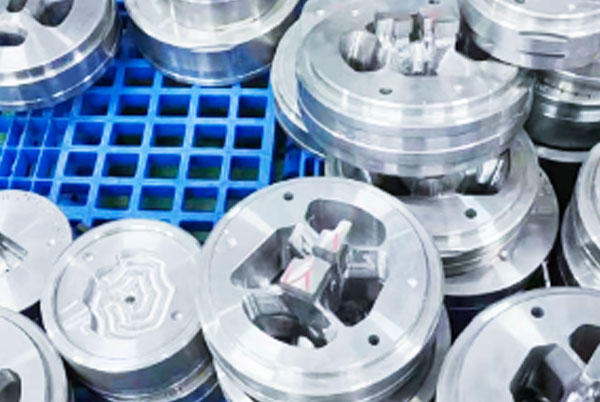
Extrusion Molds
History of Jet Mirror Polishing Machine
The jet mirror polishing technology originated from the combination of fluid dynamics and precision machining technology. It can be traced back to the end of the 20th century and was developed to meet the needs of aerospace, mold manufacturing and precision parts industries for high-finish surfaces.
This technology uses high-pressure jetting of fluid containing abrasive particles to perform non-contact polishing on the surface of the workpiece. It has the characteristics of high efficiency, controllability and non-damage. With the development of CNC technology and material science, jet mirror polishing has been widely used in high-precision manufacturing fields such as 3C product housings, medical devices, automotive parts, semiconductor packaging, etc., and has become an important part of advanced surface treatment processes.