Advanced Finishing and Polishing Machines
We supply both equipment and materials, helping you save a significant amount of time and costs!
Our surface treatment equipment is primarily used for grinding, polishing, and cleaning, including magnetic polishing machines, vibrating polishing machines, tumbling polishing machines, hub polishing machines, and advanced abrasive flow machining and fluid jet polishing machines. These machines easily process surface roughness, remove burrs, protrusions, chamfers, tool marks, scratches, coatings, and oxide layers. Especially the new fluid polishing machine, which uses flowable abrasives for deburring and polishing, completely replaces traditional manual polishing, enabling efficient batch processing. It is particularly suitable for hard-to-reach surfaces, internal structures, and complex-shaped high-precision parts.
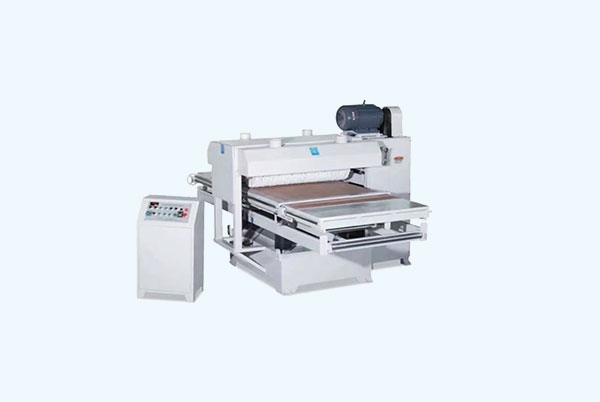
Reciprocating Polishing Machine
JC-Q01
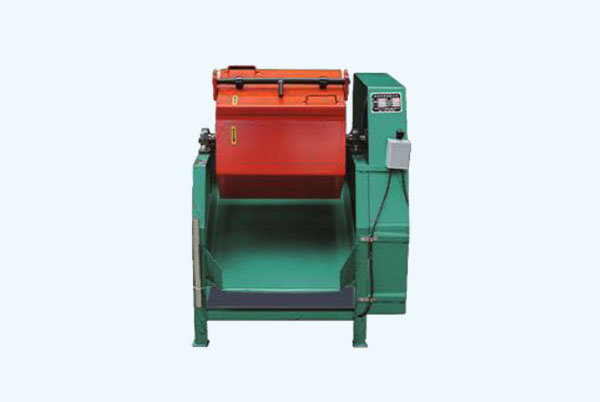
Drum Polishing Machine
JC-Q01
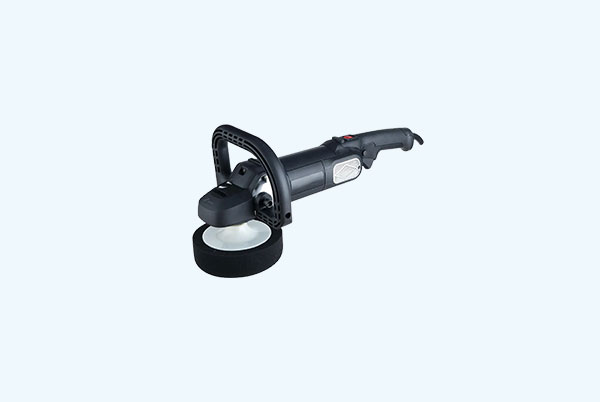
Small Car Wheel Hub Polishing Machine
JC-Q01
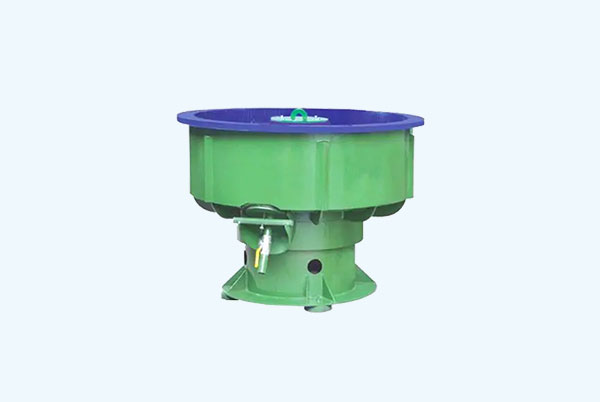
Vibration Grinder
JC-Q01

Magnetic Grinder
C2013

Horizontal Vibration Grinder
JC-Q01
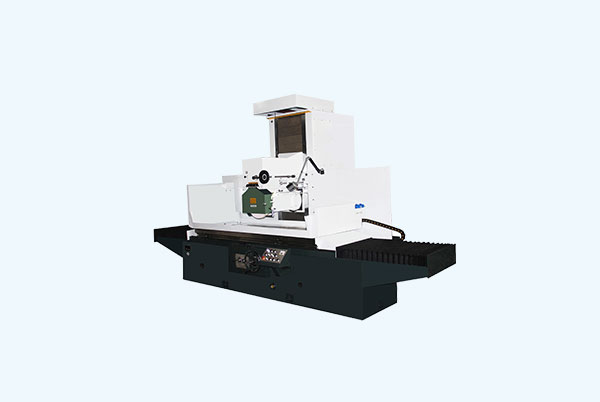
Surface Grinding Machine
JC-Q01
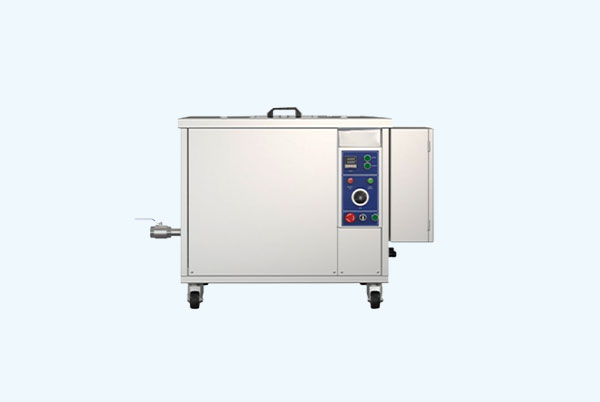
Ultrasonic Cleaning Machine
JC-Q01
Advanced and Efficient
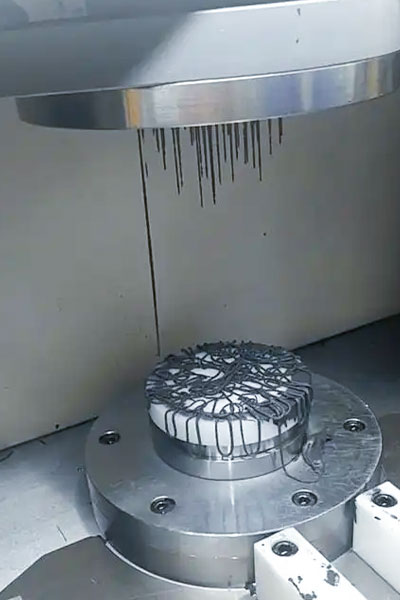
01
Consistency
02
Environmentally Friendly
03
Product Diversification
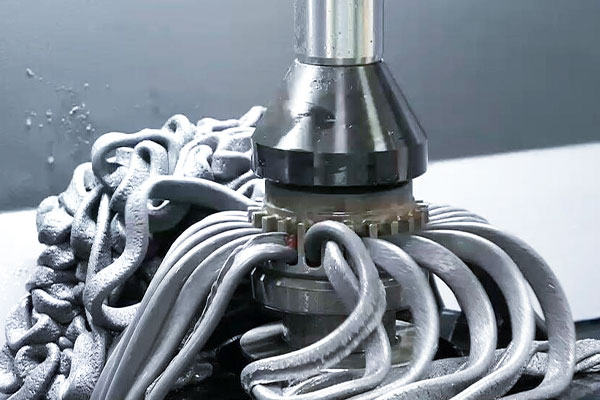
What is Abrasive Flow Machining (AFM)
Abrasive Flow Machining(AFM)involves the use of flowing abrasives that are pressed through parts to achieve a polishing effect. It is an advanced polishing machine that is rapidly replacing traditional manual deburring methods. This process can batch, quickly, and consistently handle part polishing, enhancing surface finish.
Abrasive flow machining is particularly suitable for polishing requirements of curved surfaces, internal holes, complex structures, irregular shapes, and cross-holes.
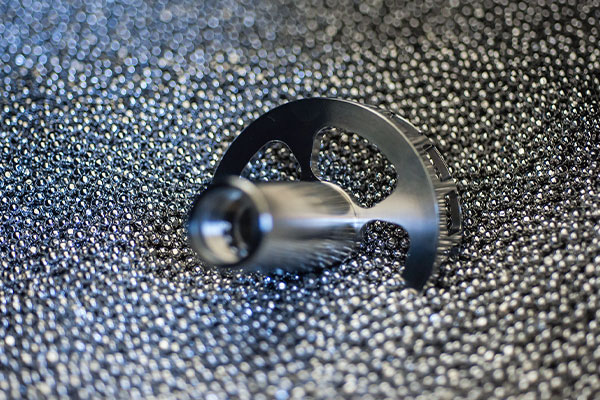
What is a Magnetic Polishing Machine?
A magnetic polishing machine is a surface treatment equipment that controls the movement of polishing media (such as steel balls and steel needles) through magnetic forces to perform precision finishing and polishing on parts. It is primarily used for deburring, surface smoothing, and removing oxide layers, among other processes.
With a high level of automation, magnetic polishing machines are widely used in the precision machining of metal workpieces.
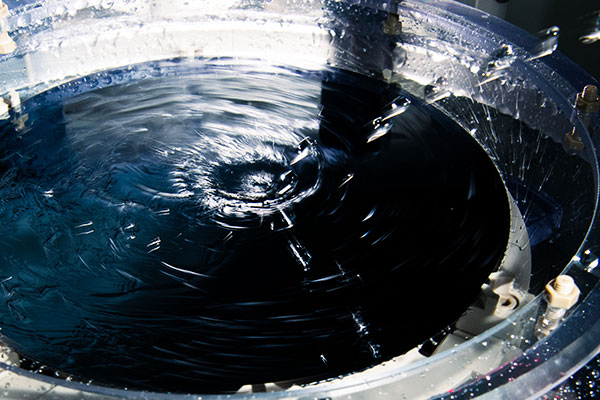
How to choose a polishing machine?
When it comes to choosing a polishing machine, the top recommendation at this stage is an automated polishing machine. After that, the selection should be based on the material, shape, and polishing standards (processing precision). Different polishing machines are suitable for different surface treatments. Additionally, it is important to consider the cost of the machine and the after-sales service.
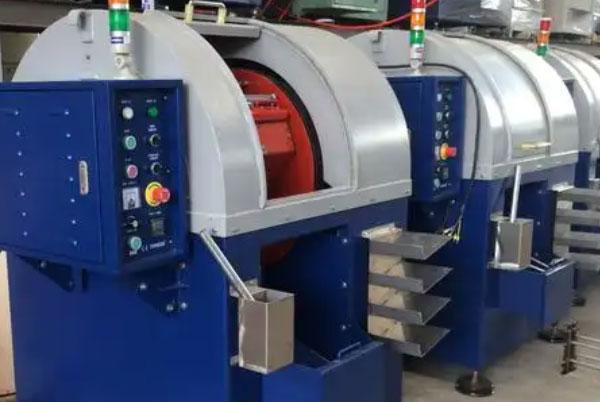
In which industries are polishing machines used?
Jichuan Chemical’s polishing machine customers are mainly concentrated in the following fields: automotive parts polishing, aerospace turbine blade parts polishing, medical device parts polishing, jewelry industry polishing, as well as the most widely used in metalworking and precision manufacturing factories.