In modern precision manufacturing, surface finishing technologies have a direct impact on product quality and performance. Traditional methods such as mechanical polishing and chemical polishing are widely used; however, they often face challenges like low efficiency and insufficient precision when dealing with complex surfaces, microstructures, or high-hardness materials.
Abrasive Flow Machining (AFM), an advanced high-precision surface finishing technology, is emerging as a critical solution in high-end manufacturing sectors such as aerospace, medical devices, and optical components, thanks to its unique processing mechanism.
So, what exactly is an Abrasive Flow Machine? How does it work? What are its applications and advantages? This article provides a comprehensive overview of AFM, covering its working principles, core technologies, and real-world applications.
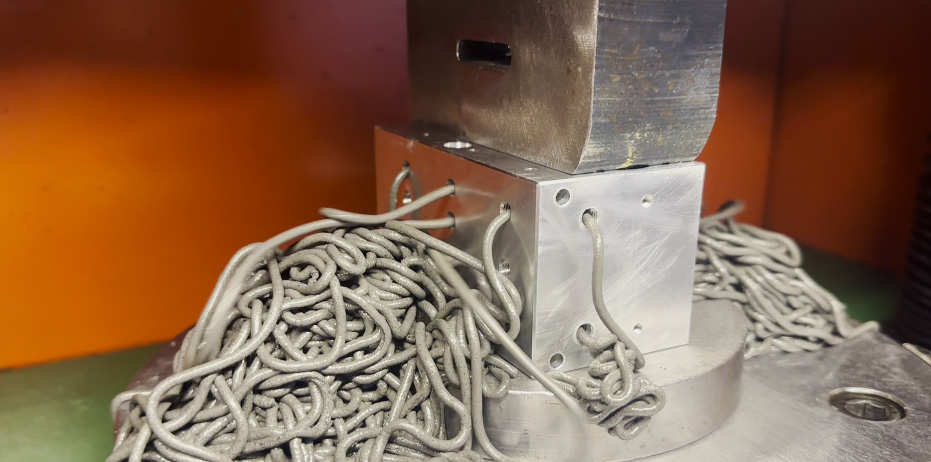
Basic Concept of Abrasive Flow Machining
Abrasive Flow Machining (AFM), also known as abrasive flow processing equipment, is a precision surface finishing technology that utilizes a viscoelastic medium containing abrasive particles under pressure to perform precision polishing, deburring, and surface finishing on workpieces. Unlike traditional polishing methods, it employs controlled abrasive flow to achieve micro-cutting on workpiece surfaces, enabling uniform processing of complex internal cavities and irregular contours while accomplishing high-precision machining without direct tool contact.
Working Principle of Abrasive Flow Machines
The core of Abrasive Flow Machining (AFM) lies in the precise control of the abrasive media. A typical AFM process consists of the following key stages:
1. Composition of Abrasive Media
The specialized media used in AFM is composed of three main components:
-
Carrier Fluid: A polymer-based medium, either silicone-based or oil-based
-
Abrasive Particles: Materials such as silicon carbide, aluminum oxide, or diamond, typically in the grit size range of #400 to #800
-
Functional Additives: Agents used to adjust viscosity, lubrication, and other properties
2. Machining Process
-
Media Filling: The abrasive media is injected into the workpiece cavity or a dedicated fixture
-
Reciprocating Extrusion: A hydraulic system drives the media to flow back and forth through the internal passages of the workpiece (typically under a pressure of 5–20 MPa)
-
Micro-Cutting Action: As the abrasive particles flow, they perform micro-removal of material from the surface’s raised areas
-
Parameter Control: Pressure, flow rate, and the number of cycles are precisely controlled and adjusted in real-time to optimize the processing outcome
Key Differences Between Abrasive Flow Polishing and Traditional Polishing
1. Working Principle
-
Traditional Polishing: Relies on rigid tools such as grinding wheels for mechanical abrasion
-
Abrasive Flow Polishing: Utilizes a flexible, abrasive-laden fluid for controlled cutting
2. Machining Capability
-
Traditional: Suitable for simple external surfaces
-
Abrasive Flow: Capable of finishing complex internal cavities and micro-holes
3. Surface Quality
-
Traditional: Achievable surface roughness of Ra 0.2–0.8 μm
-
Abrasive Flow: Can achieve ultra-fine finishes up to Ra 0.01 μm
4. Material Compatibility
-
Traditional: Prone to damaging brittle materials
-
Abrasive Flow: Suitable for a wide range of materials
5. Efficiency
-
Traditional: Labor-intensive with relatively low efficiency
- Abrasive Flow: Highly automated and efficient
In summary, abrasive flow polishing offers significant advantages in handling complex geometries, achieving superior surface quality, and ensuring consistency. It is particularly well-suited for high-precision and intricate surface finishing requirements. However, traditional polishing still holds value for simpler parts and small-batch production. As the demand for precision machining continues to grow in the manufacturing industry, abrasive flow polishing technology is seeing increasingly widespread adoption.
Jichuan Chemical’s abrasive flow machine is an advanced surface finishing solution designed for high-precision applications. Utilizing a specially formulated abrasive media, it effectively polishes complex internal cavities, micro-holes, and intricate geometries with exceptional consistency and surface quality. Ideal for aerospace, medical, and optical industries, our machine delivers automated, reliable performance for the most demanding polishing tasks.